Quality management extends far beyond mere oversight; it embodies a commitment to organizational excellence, a culture of continuous improvement, and an unwavering dedication to exceed customer expectations. Join us as we delve into the fundamental facets of a Quality Manager’s role, exploring the intricate tapestry that weaves together quality standards, control processes, compliance measures, essential skills, and career pathways in the realm of quality management.
Responsibilities of a Quality Manager
A Quality Manager serves as the linchpin in upholding and advancing the standards of products or services within an organization. Their multifaceted responsibilities revolve around guaranteeing that every facet of the organization’s offerings meets or surpasses predefined quality thresholds. They are tasked with the following:- Setting Quality Objectives: Defining clear and measurable quality objectives in alignment with the organization’s strategic goals.
- Establishing Protocols: Crafting, implementing, and overseeing protocols and procedures to maintain consistency and precision across all processes.
- Ensuring Regulatory Adherence: Staying abreast of industry regulations and standards, ensuring strict compliance, and spearheading necessary adaptations or improvements.
- Monitoring Performance: Continuously monitoring performance metrics, conducting audits, and analyzing data to identify areas for enhancement.
- Leading Improvement Initiatives: Initiating improvement projects aimed at refining existing processes, reducing defects, and optimizing overall quality.
- Team Collaboration: Collaborating cross-functionally to instill a quality-focused culture throughout the organization.
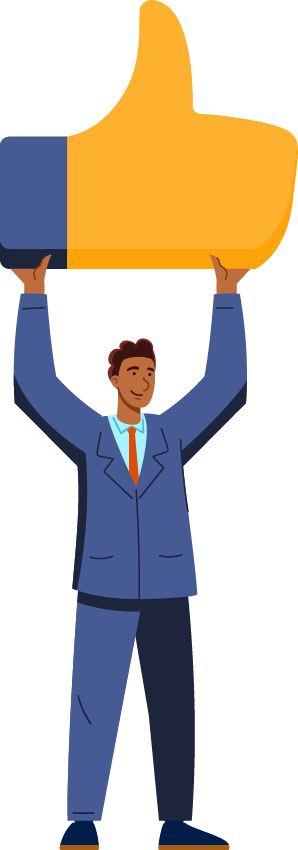
Establishing Quality Standards
Establishing and maintaining high-quality standards is essential for organizational success, impacting customer satisfaction, brand reputation, and profitability. These standards instill customer confidence, enhance operational efficiency, differentiate the organization in the market, and mitigate risks. Formulating robust standards involves leveraging ISO standards, continuous improvement models like Six Sigma, and benchmarking against industry leaders. Adaptable and measurable standards align with evolving industry norms and customer needs.
Importance of High-Quality Standards
The bedrock of organizational success lies in the establishment and unwavering maintenance of high-quality standards. These standards serve as guiding principles that permeate every facet of operations, influencing customer satisfaction, brand reputation, and overall profitability. Key reasons why quality standards are paramount include:
- Customer Confidence: Consistently meeting or exceeding quality benchmarks cultivates trust and confidence among customers, bolstering brand loyalty.
- Operational Efficiency: Well-defined quality standards streamline operations, reducing errors, waste, and inefficiencies.
- Market Positioning: Maintaining superior quality differentiates an organization within the market, giving it a competitive edge.
- Risk Mitigation: Robust quality standards mitigate risks associated with product or service failures, safeguarding the organization’s reputation.
Establishing Robust Quality Standards
Creating effective quality standards necessitates a strategic approach that aligns with industry best practices. Several methodologies and practices contribute to the formulation of robust standards:
- ISO Standards: Leveraging internationally recognized ISO standards (e.g., ISO 9001) as a foundational framework for establishing quality management systems.
- Continuous Improvement Models: Implementing models like Six Sigma or Total Quality Management (TQM) to foster a culture of continuous improvement.
- Benchmarking and Best Practices: Conducting benchmarking exercises to compare against industry leaders and adopting best practices to set ambitious yet achievable quality benchmarks.
The methods employed in setting quality standards should be adaptable, measurable, and reflect the dynamic nature of both industry standards and customer expectations.
Implementing Quality Control Processes
Quality control involves a spectrum of methodologies and tools aimed at ensuring products or services consistently meet predefined quality standards. Notable methodologies and tools include:
- Six Sigma: A data-driven approach focusing on minimizing defects and variations in processes to achieve near-perfect quality.
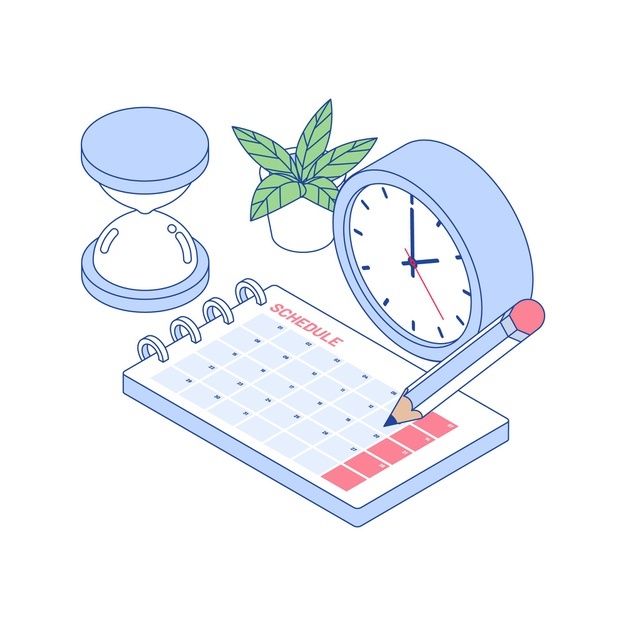
- Total Quality Management (TQM): A comprehensive management approach emphasizing continuous improvement, customer satisfaction, and involvement of all employees in quality enhancement.
- Statistical Process Control (SPC): Using statistical methods to monitor and control processes, ensuring they operate efficiently and within defined parameters.
- Failure Mode and Effects Analysis (FMEA): A systematic technique identifying potential failure modes in a system and assessing their impact.
- Lean Manufacturing: Techniques focused on eliminating waste and improving efficiency while maintaining quality standards.
Real-world examples vividly illustrate the transformative impact of robust quality control processes on organizations:
- Toyota’s Production System: Toyota’s implementation of lean manufacturing principles resulted in higher efficiency, reduced waste, and enhanced product quality.
- Motorola and Six Sigma: Motorola’s adoption of Six Sigma led to substantial improvements in product quality and cost reduction.
- McDonald’s and TQM: McDonald’s integration of Total Quality Management improved service quality and consistency across franchises worldwide.
These examples showcase how implementing stringent quality control processes can lead to significant improvements in operational efficiency, cost reduction, and overall quality enhancement.
Ensuring Regulatory Compliance
Compliance with industry regulations and standards is paramount for organizational credibility, risk mitigation, and maintaining operational legitimacy. Significance lies in:- Legal Adherence: Ensuring the organization operates within legal frameworks to avoid penalties, lawsuits, or reputational damage.
- Customer Trust: Meeting regulatory standards builds customer trust, indicating a commitment to safety, ethics, and quality.
- Operational Stability: Compliance fosters operational stability by reducing risks associated with non-compliance.
- Regular Audits and Assessments: Conducting routine audits and assessments to identify and rectify potential compliance gaps.
- Training and Education: Providing ongoing training to employees to ensure they understand and adhere to regulatory requirements.
- Integration of Technology: Leveraging technology solutions to streamline compliance tracking, reporting, and management.
- Engagement with Regulatory Bodies: Actively engaging with regulatory bodies to stay updated on changes and interpretations of regulations.

Key Skills and Qualities
In the realm of quality management, possessing specific skills and qualities is instrumental in steering organizations toward sustained excellence:
- Knowledge of Quality Management Systems (QMS): A profound comprehension of Quality Management Systems (QMS) stands as the bedrock of effective quality management. It enables a Quality Manager to establish, maintain, and optimize quality standards, ensuring organizational processes align with industry best practices and regulatory requirements. A comprehensive understanding of QMS frameworks like ISO 9001 facilitates streamlined operations, fosters consistency, and ultimately enhances product or service quality.
- Attention to Detail: Attention to detail is the linchpin in identifying potential issues before they escalate into larger problems. Quality Managers with acute attention to detail meticulously scrutinize processes, products, and services, maintaining high standards and preventing lapses that could compromise quality. This keen eye for detail ensures that every facet of operations meets predefined quality benchmarks.
- Analytical Skills: Analytical prowess empowers Quality Managers to decipher intricate data sets, extract meaningful insights, and discern underlying trends affecting quality. By harnessing analytical skills, they can identify patterns, root causes of quality issues, and opportunities for improvement. Analytical thinking facilitates informed decision-making, enabling proactive adjustments to processes for sustained quality enhancement.
- Continuous Improvement: Embracing a culture of continuous improvement is ingrained in the role of a Quality Manager. Constantly seeking areas for refinement within processes, products, or services is essential for staying ahead in an ever-evolving landscape. This commitment to perpetual enhancement ensures adaptability, fosters innovation, and fortifies the organization’s competitive edge.
Collaboration and Communication
Quality Managers operate as catalysts for collaboration, bridging departments and functions to ensure a unified approach to quality. By working across various divisions, they facilitate the alignment of goals, methodologies, and standards. This collaborative effort creates a cohesive environment where quality is a collective responsibility rather than a siloed function.
Communication stands as the cornerstone of effective quality management. Quality Managers proficient in communication skills articulate quality standards, methodologies, and expectations to diverse teams within the organization. Clear, concise communication fosters understanding, buy-in, and implementation of quality protocols across all levels and departments.
Career Path and Development
A career in quality management offers a diverse range of opportunities for individuals passionate about driving organizational excellence. Potential career paths within quality management span various roles and levels: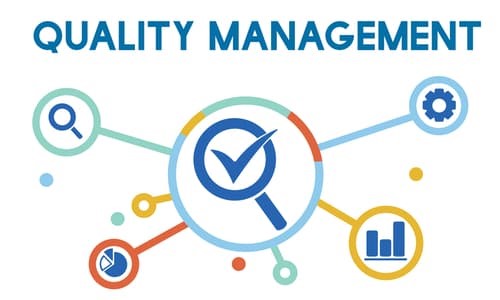
- Quality Assurance Specialist: Entry-level role focusing on ensuring products or services meet defined quality standards through testing and inspection.
- Quality Analyst/Engineer: Engages in data analysis, process improvement, and identifying areas for enhancement within quality systems.
- Quality Manager: Overseeing and managing quality control processes, establishing standards, and leading quality improvement initiatives.
- Director of Quality: Strategic leadership role, responsible for shaping organizational quality strategies and ensuring adherence to regulatory standards.
- Quality Consultant: External advisor offering expertise in implementing quality management systems and improving organizational processes.
- Certifications: Pursuing certifications such as Six Sigma, Lean Six Sigma, Certified Quality Engineer (CQE), or Certified Manager of Quality/Organizational Excellence (CMQ/OE) enhances expertise and marketability.
- Advanced Education: Obtaining a master’s degree in quality management, business administration, or related fields augments knowledge and opens doors to senior roles.
- Networking and Workshops: Engaging in workshops, conferences, and networking events within the quality management domain facilitates knowledge exchange and skill refinement.
Tips for Aspiring Quality Managers
For individuals aspiring to step into Quality Management roles, here are some actionable tips:- Education and Training: Pursue relevant education in quality management, engineering, or business administration. Consider specialized courses or degrees focusing on quality control methodologies.
- Certifications: Obtain industry-recognized certifications (e.g., Six Sigma, ISO certifications) to validate skills and expertise.
- Gain Experience: Seek opportunities to gain hands-on experience in quality-related roles. Internships, entry-level positions, or project involvement offer valuable experience.
- Soft Skills Development: Hone communication, leadership, and analytical skills. Effective quality management demands a blend of technical and soft skills.
- Continuous Learning: Stay updated with industry trends, tools, and methodologies. Engage in continuous learning through books, seminars, and online resources.
Conclusion
The realm of quality management is a dynamic landscape where precision, collaboration, and adaptability reign supreme. The role of a Quality Manager, with its diverse responsibilities, stands as a beacon of excellence within organizations, driving initiatives that shape not only products or services but also the very fabric of operational efficiency and customer trust.
Aspiring Quality Managers embarking on this journey should arm themselves not only with technical expertise but also with a deep commitment to continuous learning and holistic skill development. By fostering a culture of perpetual improvement, embracing collaboration, and aligning with regulatory standards, they pave the way for organizations to thrive in an ever-evolving global marketplace. Quality management isn’t merely a role—it’s a commitment to the pursuit of excellence, ensuring that organizations transcend mediocrity and soar towards sustained success.